February 2021 | 1 |
January 2021 | 1 |
November 2020 | 1 |
October 2020 | 3 |
May 2020 | 2 |
March 2020 | 5 |
September 2019 | 1 |
August 2019 | 2 |
May 2019 | 3 |
July 2018 | 1 |
June 2018 | 2 |
May 2018 | 23 |
2015 Willys 2.5in JKS Lift | Feb 25 2021 |
2017 Ford F350 gets a lift | Jan 28 2021 |
Lifted Adventure Van | Nov 02 2020 |
2018 Jeep Wrangler Lifted & Locked | Oct 23 2020 |
Lifted 2020 Toyota 4Runner | Oct 20 2020 |
Lifted 2019 Toyota 4Runner with Toytec | Oct 20 2020 |
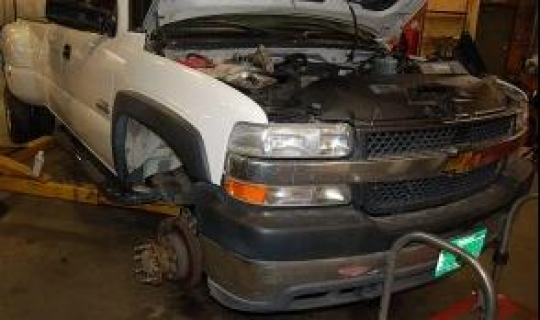
Duramax Diesel Head Repair
Duramax Heads
This 2001 Chevy 3500 Duramax has 178000 miles & is used to pull a 35’ fifth wheel trailer over long distances. The customers complaint was that it had started pressurizing the cooling system & pushing out lots of coolant.
First the tech checked the basics of the cooling system. Radiator condition & cooling ability, fan operation & then pressure test. The system cold held 20 psi for 30 minutes, which is fine. However as soon as the truck was warm it would not hold pressure at all. This pointed us in the direction of head problems. The reason it is pressurizing is that, combustion gases are getting into the cooling system & pressurizing it beyond its designed capacity.
At this point the top of the engine needed to be torn down to find the problem. As the pieces were removed they were carefully inspected for evidence of coolant or combustion on parts that should not be seeing either or.
When removing the injectors the tech found #5 was not properly seated & there were carbon deposits between the sleeve & the injector. When #8 was removed the sleeve came with it. The sleeve is supposed to be secured in the head.
When the heads came off there was evidence that combustion gases had been getting past the RH gasket at the rear. The head on this side was also slightly damaged & warped.
This news was given to the customer with the advice to put on two either new or reconditioned heads plus eight injectors & lines. Two of the injectors were no longer serviceable & with this many miles it was advisable to do them all.
Modern truck diesels are not only complicated but very time consuming to take apart & put back together because of the vast amount of plumbing they have. All the systems work at such high pressure that everything has to be in good shape to seal perfectly.
Due to the mileage of the truck the customer did not want to spend enough money for new or recon heads & ended up buying his own used heads that we checked & installed. This ended up delaying the whole job considerably because the first set of heads he brought us were not in good enough condition to put on.
The block was carefully cleaned prior to putting the head gaskets in place.
The stretch bolts that hold the head in place are now carefully torqued.
The injectors went back in the head with new copper sealing washers.
A wiring harness is attached to the injectors as they are electrically actuated.
The injectors are prepped for installation. All threads were properly lubricated prior to install. This is especially important where there are dissimilar metals involved, such as aluminum & steel.
The valve train goes onto the head next. It will be adjusted for valve clearance prior to the valve covers being installed.
The injector lines run through the valve covers.
The engine is now complete & everything must be double checked prior tostarting it.
We tried, at the customer’s preference to reuse the injector lines, but due to corrosion on some of the sealing surfaces had to replace some of the lines.
Once reassembled the truck ran properly. It has since had the other six injectors replaced & continues to give good service.